Das digitale Daten-Duplikat
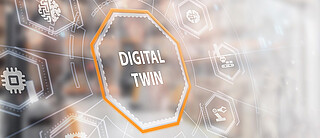
Mit dem sogenannten Digital Twin, dem digitalen Zwilling, werden Situationen aus der Realität in Echtzeit permanent in eine digitale Kopie übertragen. Daraus ergibt sich eine Vielzahl an Möglichkeiten – insbesondere in der Intralogistik und im Warenlager. Wir erklären, warum die Technologie so sehr zu kreativen Zukunftsideen einlädt.
Der „digitale Zwilling“ ist einer dieser Begriffe, die direkt unsere Fantasie inspirieren. Oft wird er mit holografischen Modellen illustriert: Servicetechniker arbeiten mitten in einem dreidimensionalen, lebensechten digitalen Abbild. „Die Realität sieht anders aus“, sagt Dennis Schüthe, Projektleiter bei STILL. Weniger faszinierend ist sie deswegen nicht. Sie erfordert lediglich etwas mehr kreative Vorstellungskraft, um konkrete Anwendungsmöglichkeiten zu erkennen.
Was ist ein digitaler Zwilling?
Im Wesentlichen lässt sich der digitale Zwilling auf folgende Definition herunterbrechen: Ein Objekt oder ein Zustand aus der realen Welt erhält ein digitales Abbild – dabei tauschen die digitale und die reale Welt konstant Daten untereinander aus. Ein klassisches Beispiel wäre eine Maschine, von der alle relevanten Informationen ständig an einen Rechner geliefert werden, damit dieser exakt darüber Auskunft geben kann, was die Maschine gerade macht und in welcher Umgebung sie sich befindet.
Ein virtuelles Abbild des Warenlagers
Der Vorteil ergibt sich aus diesem umfassenden Wissen: Ingenieure können die Maschine permanent überwachen, Manager durchgehend berechnen, welcher Umsatz zu erwarten ist, Servicetechniker können aus der Entfernung den Wartungsbedarf abschätzen. Damit hören die Möglichkeiten insgesamt aber noch nicht auf – und nicht nur Maschinen sind abbildbar. Auch von gesamten Orten und Systemen lässt sich ein digitales Abbild erstellen: zum Beispiel ein kompletter Supermarkt oder die Wasserversorgungsanlage einer Stadt – oder eben auch ein Warenlager.
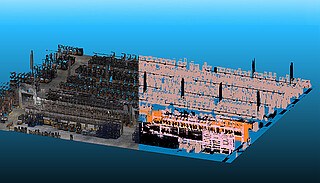
Denn auch in der Intralogistik ergeben sich durch den digitalen Zwilling zahlreiche Möglichkeiten. STILL hat dazu an dem groß angelegten Forschungsprojekt ARIBIC (Artificial Intelligence-Based Indoor Cartography) teilgenommen, bei dem mit renommierten Partnern aus Wirtschaft und Forschung getestet wurde, wie sich 3D-Karten von Warenlagern in Echtzeit darstellen lassen. „Das ist die Grundlage für die Intralogistik der Zukunft“, sagt Schüthe. Das Besondere daran: Die digitale Karte soll nicht nur Datenpunkte erfassen, sondern diese auch interpretieren: „Ist es eine Person, eine Palette oder ein Feuerlöscher?“, beschreibt Schüthe. Mit dieser Datenbasis und einer entsprechenden Software wäre das möglich, was Warenmanagementsysteme (WMS) schon seit vielen Jahren versprechen, in der Praxis aber oft nur unzureichend umsetzen: Warenflüsse, Verkehr oder Auslastung könnten punktgenau in Echtzeit verfolgt werden. In der Realität scheitern die bisherigen Programme oft zum Beispiel am „Faktor Mensch“, wie Schüthe ausführt: „Wenn das WMS dir vorgibt, dass eine Palette an einer bestimmten Stelle eingelagert wird, aber die Mitarbeiter vor Ort sich darauf einigen, dass das Regal darunter viel praktischer und meistens leer ist, hilft derzeit keine Software.“
Sensoren sammeln Daten
Ein vollständiger digitaler Zwilling des Lagers könnte dementsprechend Intralogistikern in der Zukunft ganz neue Möglichkeiten eröffnen: Produkte ließen sich in Echtzeit verfolgen, komplette Lagerarchitekturen basierend auf den Datensätzen umbauen und perfektionieren. Dienstleiter wie STILL könnten ihre Optimierungsvorschläge passgenau aus der Ferne erarbeiten und durchplanen, ohne dazu zeitaufwändig vor Ort Beobachtungen anzustellen. Noch ist das Zukunftsmusik und wird insbesondere davon abhängen, wie gut sich entsprechende Software-Applikationen entwickeln lassen – und wie umfassend die Datenbasis ist.
Denn der Erfolg eines Digitalen-Zwillings-Modells steht und fällt in allen Anwendungsbeispielen mit der Datenbasis. „Im Grunde reden wir beim digitalen Zwilling, sehr vereinfacht gesagt, von einer Datenbank“, beschreibt es Schüthe. Diese Daten müssen nicht nur von einer künstlichen Intelligenz analysiert und interpretiert werden – sie müssen vor allem sinnvoll und umfassend erhoben sein. Entscheidend sind also Sensoren: Je nach Anwendungsbeispiel müssen sie nicht nur visuelle Informationen messen, sondern auch Temperatur, Druck, Beschleunigung oder Gravitation. Eine entsprechende Datenbank zu erstellen, ist alles andere als trivial – auch dazu galt die Forschung bei ARIBIC.
Digitaler Zwilling verbessert den Service grundlegend
Die vielfältigen Vorteile dieser Technologie nutzt STILL zum Beispiel bereits im Service bei automatisierten Fahrzeugen. Der digitale Zwilling unterstützt die Servicetechniker in ihrem Alltag: Komponenten können passend für ein Fahrzeug konfiguriert und dann in der Cloud gespeichert werden. „So ist sichergestellt, dass der Techniker immer die korrekte Software auf dem dazugehörigen Fahrzeug hat“, sagt Hubert Klosterberg, Service Expert bei STILL. Dabei spielt vor allem die Standardisierung von Software und Hardware eine entscheidende Rolle: „Wir müssen Techniker nicht mehr auf ein Projekt speziell ausbilden.“ Jeder geschulte Techniker kann dann künftig die standardisierten Aufgaben bei jedem Kunden durchführen. Hinzu kommt: Mit dem digitalen Zwilling können die STILL Servicetechniker neue Hardware schnell und unkompliziert mit einem Back-up aus der Cloud konfigurieren und direkt vor Ort einbauen: „Das erhöht die Verfügbarkeit der Fahrzeuge signifikant“, so Klosterberg. Darüber hinaus ist es möglich, die Produkte kontinuierlich zu optimieren.
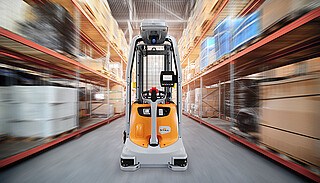
Eine auf den ersten Blick völlig andere Anwendung ist das Projekt „LernFFZ“. Die Idee: Autonome Fahrzeuge sollen von realen menschlichen Fahrern lernen, wie sie sich verhalten. „Vergleichbar in etwa damit, wie Eltern ihrem Kind etwas demonstrieren, damit es das nachahmt“, sagt Lukas Hindemith, Projektleiter bei STILL. Dazu muss der Stapler zunächst einmal mit möglichst vielen Situationen gefüttert werden, insbesondere in Manövern, Bewegungen und Grenzfällen, die nur selten vorkommen. Dazu baut STILL derzeit einen Simulator als digitalen Zwilling, der anschließend von menschlichen Fahrern gesteuert wird. Mehr noch: Die automatisierten Fahrzeuge müssen anschließend idealerweise selbstständig neue Fahrstrategien lernen. „Das gelingt nur wirklich gut, wenn auch möglichst viele Fehlschläge dabei sind“, beschreibt es Hindemith: „Aus Fehlern lernt man – das gilt auch für das Fahrzeug.“ Das Fahrzeug trainiert also als virtuelles Abbild. Schließlich möchte niemand reale Lager und Stapler beschädigen.
Training in der virtuellen Spiegelwelt
Diese Überlegung ähnelt einem wiederum anderen Anwendungsfall: dem Schweißsimulator in der Ausbildung von Konstruktionsmechanikern bei STILL. Der Schweißhelm, den sich die Auszubildenden aufsetzen, verfügt hier über einen Bildschirm. Die reale Umgebung verschmilzt mit der Simulation. Durch die Augmented-Reality-Simulation wird aus Kunststoffplatten massives Stahlblech und aus einem Kunststoffklotz eine Schweißdüse. Der Vorteil: Es kann nicht nur ohne Hitze und Rauch trainiert werden, also auch ohne aufwendige Schutzausrüstung – die Auszubildenden erhalten gleichzeitig in Echtzeit Rückmeldung, wie schnell sie arbeiten, welchen Abstand und Winkel sie einnehmen und wie sie sich korrekt positionieren. „Der Augmented-Reality-Schweißsimulator trainiert das Muskelgedächtnis mit einer besonderen Tiefe“, sagt Maximilian Schwenn, Ausbildungsmeister bei STILL. „Das wäre sonst nur gleichzusetzen mit einer intensiven Eins-zu-eins-Betreuung.“ Die Unfallgefahr ist verringert, der Materialverbrauch wird deutlich reduziert und die Auszubildenden lernen nachweislich deutlich schneller: „Selbstverständlich sieht die erste Schweißnaht unter Realbedingungen in der Schweißkabine nicht wie auf dem Simulator aus“, erläutert Schwenn, „aber die veränderte Umgebung wird schnell in das Gelernte adaptiert und so können großartige Ergebnisse erzielt werden.“
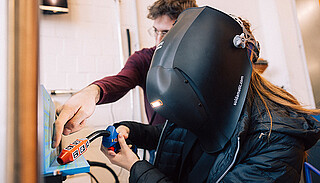
Ein digitales Abbild eines Warenlagers in Echtzeit, eine virtuelle Kopie eines Staplers oder ein perfekter Trainingssimulator – keine dieser fantasieanregenden Ideen ist das eingangs beschriebene 3D-Hologramm. Aber die Vielfalt dieser Möglichkeiten zeigt bereits auf, in welche verschiedenen Richtungen die Technologie noch genutzt werden könnte. Entscheidend für weitere Anwendungen wird unter anderem auch die Kreativität von Dienstleistern wie STILL sein – insbesondere im Zusammenspiel mit den Ideen und Anforderungen der Kunden für ihre jeweils individuellen Lösungen. Auch wenn also manche Benutzeroberfläche auf den ersten Blick eher dem Charme einer Tabellenkalkulation gleichen mag, sollte sich davon niemand täuschen lassen: In wenigen Technologien steckt für die Intralogistik wohl aktuell so viel Zukunftsvision und kreative Möglichkeit wie im digitalen Zwilling.
Kontaktanfrage
Abonnieren Sie unseren Newsletter!
Mit STILL immer auf dem Laufenden: Bestellen Sie den STILL-Newsletter und wir informieren Sie regelmäßig über interessante Branchenthemen.