Level up! Smart processes in intralogistics
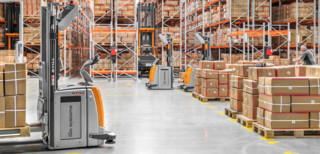
Process optimisation is essential in intralogistics. Dynamic markets, constantly changing requirements and a shortage of skilled labour make it necessary to critically examine existing processes. STILL supports its customers in this process - with decades of expertise, smart solutions and innovative technologies.
In the dynamic environment of modern markets, a company's ability to adapt and grow is critical to its success. As a result, many intralogistics companies are focusing on making their processes as flexible and scalable as possible in order to respond efficiently to unexpected changes. After all, intralogistics in particular is subject to constant change and is also a critical element of the supply chain. Process optimisation is not completed in a few steps, but is an ongoing process.
Customised solutions
Intralogistics is a very fast-paced business that is under great time and financial pressure. There is rarely an opportunity to take a step back and review the processes in detail. It therefore makes sense to call in a reliable partner for intralogistics processes. STILL assists its customers in a spirit of partnership and supports them on their way to more flexible and intelligent processes. "We take a close look at our customers' needs and offer them individual and customised solutions," emphasises Florian Heydenreich, Executive Vice President Sales & Service at STILL.
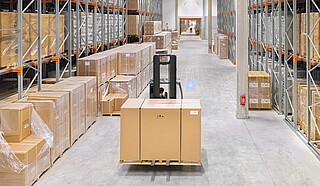
This is why every process optimisation starts with a detailed analysis of the existing material flow and logistics processes. The aim is to identify strengths, potentials and weaknesses, and, in the next step, to derive targeted individual measures and solutions for the warehouse. "Many processes become more flexible and scalable with the implementation of innovative technology," explains Heydenreich. Even though this process may involve significant changes in some cases, it pays off in the long term through increased efficiency. STILL has a broad portfolio of smart solutions for intralogistics, covering all areas of the warehouse - from incoming goods, order picking or production supply to outgoing goods. All solutions are summarised on the STILL website under "Smart logistics processes". This clearly illustrates the possibilities for process optimisation offered by STILL's innovative technologies.
Measurability and flexibility
The intralogistics industry is also strongly determined by key performance indicators (KPIs), i.e. decisive performance indicators that can be used to analyse and optimise logistics processes. This also requires logistics companies to know how busy their vehicles are, how long order pickers need per pick and what goods are located where in the warehouse. To precisely record all of this, STILL uses material flow and fleet management systems. The fleet management system can, for instance, identify whether more vehicles are actually needed to load the goods - or perhaps different vehicles. The integration of such management systems leads to more transparent processes that can be better understood and optimised. It is also easier and quicker to react to changes if the entire process or individual process steps are digitally mapped.
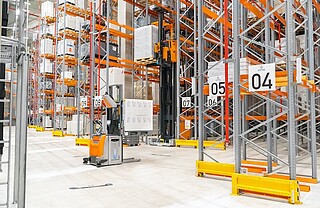
Automated industrial trucks offer additional flexibility. Firstly, companies are less dependent on the availability of skilled staff on the labour market. Secondly, existing staff can be reassigned from repetitive and monotonous tasks, freeing up capacity for more complex and demanding processes. Another benefit is that automated trucks can make better use of existing space - particularly important when there is no room for further warehouse expansion. Costs can also be reduced and existing resources used more efficiently.
Modernise existing infrastructure
However, not all areas need to be changed at the same time to achieve a more efficient process. Even the optimisation of a single work step can lead to an improvement in the overall material flow. This can be achieved by integrating new technologies into the existing warehouse infrastructure. Retrofitting existing systems is a successful way to gradually modernise and develop your own systems and make them more secure in the long term. "We help our customers to identify where there is the greatest potential for optimisation. The retrofit can then be extended to other processes step by step," says Heydenreich. Regardless of which processes are to be optimised and to what extent smart solutions are to be implemented, STILL is always at its customers' side as a reliable and competent partner.
Contact request
Subscribe to the Newsletter !
Always up to date with STILL: Subscribe to the STILL newsletter and we will inform you regularly about interesting industry topics.