Smart service for automated equipment in intralogistics
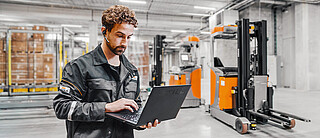
STILL supports its customers - from planning to commissioning and maintenance. Service plays a decisive role. Whether remotely or on site in the warehouse: STILL has the right expert for every challenge. Even around the clock, if necessary.
"The demand for automation solutions in intralogistics is high, especially in times of skilled labour shortages," explains Patrick Litz, Head of Advanced Applications for the German region. In most cases, however, companies do not have automation experts in-house. But they are needed to design and commission automated systems. "At STILL, we recognised this early on and built up a large network of in-house automation experts," continues Litz. They support customers in the planning and implementation of STILL automation solutions.
Comprehensive range of services
And STILL continues to support its customers after the implementation of an automation solution: "We offer our customers a comprehensive range of services that goes far beyond commissioning," explains Kai Eilers, Regional Service Manager. This offer is divided into different areas. The first contact is usually via Remote Support, where trained service personnel receive customer enquiries. "We can often help remotely without someone having to travel to the customer's premises, especially when it comes to software," says Eilers. Trained staff can access the vehicles in the customer's system via a digital interface. Of course, there are some problems that can only be solved on site. In this case, Remote Support forwards the problem to the STILL service technicians. Eilers emphasises: "We provide them with as much information as possible, so that ideally they can go to the customer and bring the right spare part with them". This minimises potential downtime and saves the customer costs.

Avoid downtime
"Many customers are already concerned about system availability when planning automation solutions," says Litz. No wonder, because switching to automation solutions such as automated guided vehicles (AGVs) or autonomous mobile robots (AMRs) usually involves an initial investment. Delays or failures are therefore particularly painful. "That is why service is so important to us at STILL," emphasises Litz. "Depending on the customer's requirements, our service team is available up to 24 hours a day, seven days a week. This team also includes the automation experts mentioned above - they are available in all STILL offices. In the event of complex problems, they are quickly on site at the customer's premises. The majority of customers rely on this rapid assistance from STILL Service - to varying degrees. "Thanks to our different levels of support, we can guarantee high system availability - an important factor for intralogistics companies," explains Litz. "Often there is no specialised staff available within the company. The fact that we provide this service alongside the system is highly appreciated.
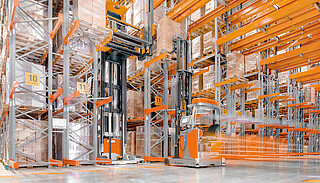
Improve storage efficiency
But the STILL experts don't just help with problems, as Litz explains: "Because in an automated warehouse, customer support does not end immediately after commissioning". The automation experts can also help the system operator to further optimise the system at a later date. The right software helps them to do this. The company's own analysis tool, iGo insights, is directly linked to the warehouse's transport control system and can derive specific recommendations for action from the information collected, if necessary. "With our services, we keep an eye on the whole system," says Litz. An acute problem needs to be solved quickly: "It's just as important to look at the processes and analyse what led to the malfunction." In this way, warehouse efficiency can be further improved even after automation solutions have been introduced.
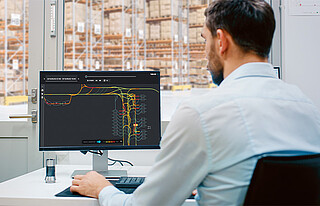
"We are always looking for ways to expand our portfolio," says Litz. This includes equipment and software development, of course, but also service: "Automated warehouse solutions are becoming more and more comprehensive and complex. That's why it's crucial to have a competent partner at your side for project development and support. And the experts at STILL demonstrate this automation expertise in many projects every day.
Contact request
Subscribe to the Newsletter !
Always up to date with STILL: Subscribe to the STILL newsletter and we will inform you regularly about interesting industry topics.