Preventing forklift trucks from tipping
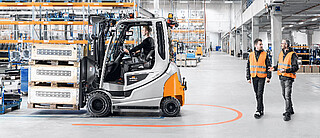
Sobering reality: A considerable number of accidents involving trucks still occur every year. Many of these accidents could be avoided with the right precautions. A more in-depth look at the causes and the best solutions.
Why are accidents with forklift trucks so dangerous?
Even though at first glance they may seem like sedate and slow assistants, industrial trucks do in fact combine an enormous amount of power and weight. The standard forklift is three times heavier than the average car but can still travel at around 20 kilometres per hour. With this amount of power, it could knock down a small wall. Furthermore, its brakes are located at the front, but its counterweight is at the rear, which makes it tricky to manoeuvre. What’s more, a forklift doesn’t just drive around the warehouse, it is usually loaded, more often than not with a heavy load. “It is still tipping accidents that result in the most serious and sometimes fatal accidents,” explains Jürgen Wrusch, Product Trainer for Counterbalance Trucks.
How much damage do forklift accidents cause each year?
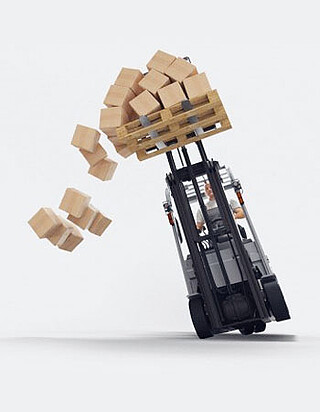
It’s hard to quantify, but it is immense. It is no wonder – in Germany alone, more than 30,000 accidents occur each year involving forklifts, pallet trucks or other industrial trucks. This figure has remained remarkably constant over the past few years, including 2020, which actually saw a decline of around 13 percent in reportable workplace accidents due to the pandemic. This resulted in ten fatalities in Germany. In other countries, the figures are proportionally similar – there are around 90 deaths per year in the USA, for example.
It is difficult to calculate the damage because it is usually multifaceted. On the one hand, there are costs associated with property damage or repairs, but there are also costs arising from employee absences due to injury: “A workplace accident in the warehouse costs an average of 1,000 euros per day in terms of personnel alone,” continues Wrusch. This does not even include the costs resulting from delivery failures, delays or the damage to the company’s image.
How many of these accidents could be prevented?
“The vast majority for sure,” estimates Wrusch. In fact, based on the data available, it is quite easy to see what the causes of accidents are in each case. Very often it is carelessness, inadequate forklift training or simply the layout of the warehouse – poor visibility of the surrounding area or badly planned vehicle movement. “Particularly in areas where there are a lot of vehicles moving around, the risk of collisions is enormous,” says Janos Poppe, Product Trainer for Warehouse Technology. Unfortunately, you also get employees who behave recklessly. In other words, employees who foolishly organise races or operate the forklift even though they are not authorised to do so – even sometimes under the influence of alcohol.
Where does the first step to increased forklift safety begin?
Before the truck is even driven. It’s possible to reduce risks through proper training and a thorough analysing the warehouse’s danger points. There are also quite simple measures that can be taken to prevent the wrong person from driving the truck and to ensure that a forklift with a technical defect is not driven in the first place. This can be done with pre-shift checks, i.e., systems in place that require the operator to undergo a safety check, personal identification or even an alcohol test. “These procedures can be of particular benefit to inexperienced users when they carry out their daily operational checks,” explains Wrusch. “Many accidents are the result of distracted or negligent operators.” This type of behaviour is often triggered by fatigue or alcohol consumption. Access controls can also be used to manage such risks. Another solution would be to have individual user profiles that, for example, only allow experienced employees to load goods at considerable heights: “You can tailor the vehicle’s features to suit each individual employee,” explains Wrusch.
What can be done to prevent speeding?
With their sensors, modern systems can measure a wide range of parameters and intervene, if necessary, using the vehicle’s control system. For example, the system can reduce the truck’s speed. “If an operator is carelessly speeding over potholes or concrete bumps, the sensor will detect these jolts,” explains Wrusch. “In response, the vehicle will be slowed right down without the operator being able to override it.”
How do we protect the operator from employees not paying attention?
Indeed, it is not always the operators who are to blame for accidents. Pedestrians are just as likely to disregard the walkways or fail to notice the electric forklifts that operate so quietly. This is where light signals or warning tones can help. They alert pedestrians to the presence of the truck from a distance. Incidentally, this is an aid that can also benefit the operator – similar to the warning sensors fitted all over cars nowadays. “However, these sensors are best suited for environments with a lot of space and little traffic,” adds Wrusch. Otherwise, alarms will be going off all the time.
Are there any comprehensive solutions that tackle multiple hazards at the same time?
Yes, there are. Safety systems using radio waves help to minimise the risk of accidents throughout the warehouse whilst providing interesting and diverse approaches to managing risk. To do this, vehicles, pedestrians and also some fixed installations are equipped with radio modules. Should vehicles or pedestrians cross each other’s path, both are warned. Similarly, the system can warn operators with raised forks when they approach a gate that is too low. “Should this be the case, the system can stop the vehicle immediately,” explains Wrusch. “Anything higher won’t get through.” Wrusch himself was once witness to an incident in which an operator only realised afterwards that their mast had been extended too far. “The structure survived, but the gate didn’t. It made the hall inaccessible during repairs,” he recounts. This was a costly oversight.
Are these measures also possible without the need for complex installations?
Definitely – if it’s just a matter of high-speed risk, then ultrasonic sensors work just as well. These are installed on the roof of the vehicle. “This is particularly useful when operators switch between outdoor and indoor driving,” explains Poppe. “Outside, of course, the operator is usually allowed to take full advantage of the vehicle’s performance.” The sensor takes over the task of remembering that this can lead to problems when driving inside.
And how do you prevent the tipping accidents mentioned at the beginning of this article?
Again, by using assistance systems. The most frequent cause of trucks tipping over is that the operator misjudges the truck’s centre of gravity. What is known as the forklift’s “stability triangle” is sometimes difficult to grasp, even for experienced operators. Even after training, many people still don’t quite understand that the stability of their square truck is actually based on a triangle meaning they calculate their own centre of gravity incorrectly. If they drive around a bend too fast or lift loads that are too heavy too high, they will tip over. “However, you can avoid this problem relatively easily with assistance systems,” says Wrusch. They handle the calculations, causing the vehicle to brake automatically or resist extending the mast too far. Assistance systems can also prevent the mast from swaying. “When you’re stressed, you make mistakes,” emphasizes Poppe. The fact that operators occasionally fail to pay attention in their daily work can probably never be completely prevented, but with the right precautions, it is certainly possible to avoid dangerous and costly accidents.
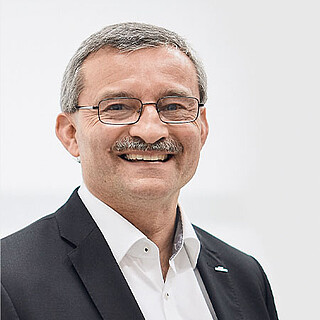
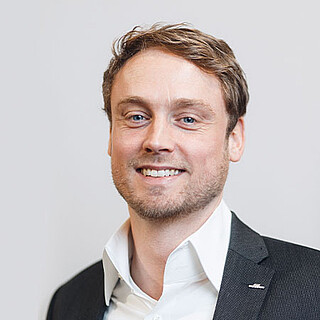
You can learn more about safety and the wide range of smart solutions that can prevent accidents and damage here in the STILL webinar that took place in May 2021.
Contact request
Subscribe to the Newsletter !
Always up to date with STILL: Subscribe to the STILL newsletter and we will inform you regularly about interesting industry topics.