How to improve warehouse efficiency, an expert guide by STILL
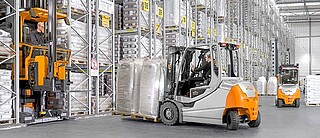
Efficiency is second only to safety on the list of priorities when it comes to a well-run warehouse. But how can you improve efficiency as a warehouse or logistics manager? Here are our top tips including expanding storage space, the use of warehouse management systems, cubing, lean inventory management and the use of automation.
What tips would you give for improving materials handling efficiency?
In simple terms, materials handling efficiency can take two forms: it can be the product itself that’s being moved, or it can be the method of moving it. A lot of the time, most issues arise from a mismatch between those two.
When we work with a customer, we take a consultative approach, we spend time with them initially to understand where they see their potential pitfalls. Our top tip would be to take a closer look at everything you’re doing and consider each stage of the process.
There are all sorts of avenues you can explore when it comes to improving materials handling efficiency. It’s about getting information, making sure that the information you have is up to date and accurate and then evaluating it accordingly. Then try to factor in any future-proofing to create a plan that shows improvements in both the short and long term.
Very few warehouses work at maximum capability, we would estimate that 90% of the marketplace can achieve a significant degree of improvement. Any investment in sustainable improvements will be paid back over time. Improvements can come in many forms, such as via optimised racking systems, the use and selection of material handling equipment or a mixture of both. Sometimes it can be as simple as just training your employees to operate their equipment more efficiently and safely in order to reduce damage.
How can you efficiently expand storage space in a warehouse?
There are numerous ways of expanding storage space. The principle criterion is the physical size of the building. Understanding the loads that the warehouse needs to store, and the movements of those loads will then help you determine if the current storage system is suitable for you today, and in the future. It may be that some small changes need to be made so that your storage space simply performs better.
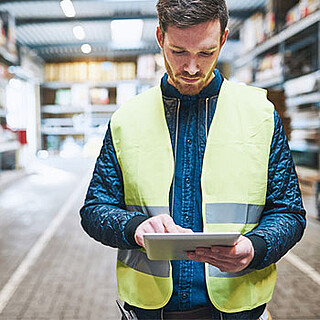
Often, the process of expanding storage tends to require a bit more in-depth analysis. We may look at alternative racking solutions or alternative handling solutions. Sometimes that will be transferring to a shuttle racking system or perhaps a live storage system. We look at all possibilities, including the use of industrial trucks or material handling equipment and automated systems – the choices are very varied and individually tailored to the customer’s needs.
The aim is to make the solution as simple and efficient as possible. It’s about what’s achievable and what’s affordable for our customers. At the end of the day, you need to be in a position where you can make the step changes at a pace that suits you.
How does a Warehouse Management System improve efficiency?
The interesting part about a Warehouse Management System (WMS) is that it can be anything from an Excel spreadsheet, through to a completely intuitive and automated piece of software. There are several generic items that you need within a Warehouse Management System (WMS) for it to work for you. The beauty of modern software is it really can be tailored to the needs of a specific system, but the basics are ultimately to make sure that you manage waste and improve productivity in the warehouse. The WMS should measure and control what’s coming into the warehouse.
It generally produces the paperwork and stocking labels. It will often also create the picklist and the route for the picker to follow.
It covers the management of stock, so that reports can be generated by the management teams. For example, it will show if a product is growing or declining in popularity. Those are the sort of benefits that a good Warehouse Management System (WMS) will give you.
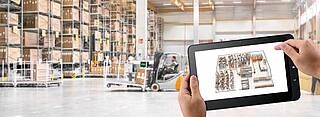
What is ‘cubing’ in warehouse management?
‘Cubing’ is an offshoot of the Warehouse Management System (WMS). For it to be of benefit, the system needs to be aware of each product location, whether that’s a simple pallet location or a more complex layout. Some warehouses will have a very simple setup, e.g. all the racking is the same, all the pallet locations are the same. Others will have different layouts depending on the types of products and their turnover.
‘Cubing’ allows you to identify the different pallets of various shapes and sizes in the warehouse, and then tries to allocate them to the most appropriate pallet location. This can take a little more investment initially to set up but it’s more efficient over time, particularly for warehouses with a lot of uniformly sized products.
How does lean inventory management work?
Lean inventory management is an adjacent Warehouse Management System (WMS). You need a good strong WMS, and all the protocols that go with that. Lean inventory management helps to maintain the right balance of stock, based on how that stock needs to be processed.
Let’s say that there are three different products which need to be ordered at different intervals. Product A is ordered on a monthly basis, Product B on a quarterly basis and Product C on a bi-annual basis. Depending on where the products are coming from, what the lead time is and what the shipping time is, these will need to be handled differently. Lean inventory management allows you to manage that stock balance and only store what you need to, in order to increase the efficiency of the warehouse.
It also gives you the opportunity to have a perpetual stock control system in place, so that you can better understand your cash management and the impact on the cash flow of the business. If it is programmed properly, it also allows you to manage the life expectancy of a product to reduce wastage.
How is automation improving warehouse efficiency?
Intralogistics automation is geared around doing the routine jobs reliably and consistently without mistakes. Your employees can focus on tasks that require a higher level of responsibility. They can fine tune the processes and adapt them as required.
At the extreme end of automation, you have very few operators and they are observing and managing the system. There are also often only a few storage areas where automation makes sense. There are also elements of automation which work in combination with operators on the floor, for example using autonomous pickers such as the OPX iGo neo or automated reach trucks which can be flipped into manual mode, giving you full flexibility to adapt.
With properly planned automation, if the amount of material being handled increases, you can simply add more equipment, because the system in place will ensure everything works together seamlessly.
The growth in automation has been driven by several factors but it’s been brought to a head in the last couple of years. The pandemic has also led to fluctuations and vagaries of people being available to work. So, by using automation, a company can be impacted much less by these types of external factors whilst still improving efficiency.
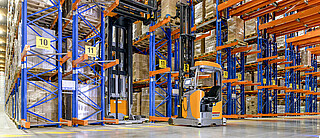
Find out how our professional team can help
We can help your business improve warehouse efficiency. If you need advice on any of the topics mentioned above, please feel free to contact us.
Contact request
Subscribe to the Newsletter !
Always up to date with STILL: Subscribe to the STILL newsletter and we will inform you regularly about interesting industry topics.