Focus on circularity: Circular economy at STILL
Circularity is nothing new for STILL - from refurbishment and battery recycling to a forklift truck based on the cradle-to-cradle principle. Frank Müller explains why circularity concepts have a long tradition at the company.
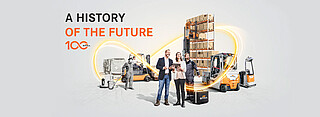
What is circularity? A circular economy in which there is no waste and all resources can be reused. This is the aim of the circularity concept, an economy based on the principles of reduce, reuse, recycle. "The objective is to keep as many resources as possible in circulation," explains Frank Müller, Senior Vice President Sales & Service Business Development STILL EMEA. In the long term, this reduces CO2 emissions and protects the environment.
Company-owned reconditioning centres
STILL has a long tradition of circularity, as company founder Hans Still began his career repairing electric motors. "The concept of circularity was there right from the start: I repair something that already exists," explains Müller. And STILL continues this tradition today: "We have our own factories all over Europe that specialise in reconditioning our trucks". In this way, STILL gives industrial trucks a second or even third life. The company has been operating these reconditioning centres since the 1980s and is constantly expanding its range of services, as Müller explains: "In the factories, the trucks are dismantled and the individual parts are inventoried. The trucks are then classified and only those parts that really need replacing are replaced. As early as 2003, STILL introduced clear guidelines for the classification of reconditioned trucks. Based on five criteria, such as technology or battery condition, the trucks are classified as bronze, silver or gold to give the customer a clear overview of the truck's condition. "Transparency is very important here," says Frank Müller. The entire lifecycle of a vehicle can be 20 years or more.
"The used trucks meet STILL's high quality standards. To the naked eye, a forklift truck that has been reconditioned by us is almost indistinguishable from a new truck," says Müller. And the durability, especially of the reconditioned gold class trucks, is almost the same as that of a new forklift truck.
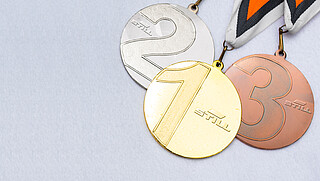
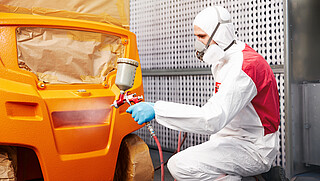
Do you want to learn more about STILL's reconditioning centres? Click here for the press release: Read more.
The cradle-to-cradle principle
But STILL does not stop there. "If you take circularity one step further, you end up with cradle-to-cradle, which means from source back to source," says Müller. Under this principle, at the end of its life, a product is broken down into its original materials, which are then returned to their respective cycles. It is important to use the materials in such a way that they can be cleanly separated again. This also means avoiding composite materials throughout the product that cannot be reprocessed: "We are already working on a concept study with our RXE series," says Müller. The goal: a forklift truck that is ideally 100% recyclable.
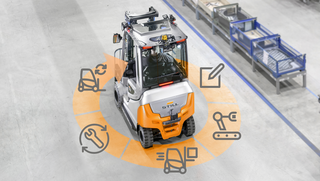
"To achieve this ultimate form of circularity, you have to start at the product design stage," he explains. "We look at every part of the vehicle: Is it really needed? And if so, can we produce it in a sustainable way?" says Müller, outlining the process. Wherever possible, recycled or biodegradable materials are used: "We also want to achieve traceability of all components and provide conclusive information on how they are recycled." A circular forklift truck must meet all these requirements if it is to achieve cradle to cradle certification. "In the spirit of transparency, however, I would like to point out that the RXE is still in the design phase," emphasises Müller.
Sustainable battery recycling
STILL already has a sustainable solution for customers in another area: the recycling of lithium-ion batteries. "Together with our partner Li-Cycle, we ensure that the most important materials from our lithium-ion batteries remain in the cycle," says Müller. Li-Cycle uses the so-called "Spoke & Hub" process: In this process, the batteries are first shredded under water and then materials such as lithium carbonate, cobalt sulphate and nickel sulphate are recovered from the resulting mass. "The process is particularly environmentally friendly as it produces very low CO2 emissions and residual materials," explains Müller. "We are already preparing to return the recovered materials to our lithium-ion cell suppliers and use them to manufacture new batteries. In this way, the valuable resources will remain in the cycle in the future. "This makes us a pioneer in the materials handling industry and contributes to the establishment of a circular flow economy for lithium-ion batteries in Europe," explains Müller. STILL is already working on complying with the new EU battery regulation.
Focusing on the entire value chain
The EU Commission's Green Deal stipulates that all collected batteries must be recycled from February 2024 in order to increase the utilisation ratio of the materials they contain. "Lithium-ion technology is still quite new, which is why STILL does not have a lot of returned batteries at the moment," says Müller. "This makes it all the more important that we start our cooperation with Li-Cycle now. This is also part of STILL's service commitment, as he explains: "Whether it is battery recycling or the industrial reconditioning of used trucks, we offer our customers sustainable solutions".
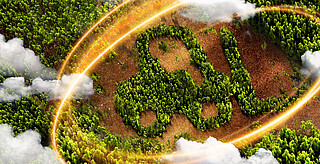
STILL looks at the entire value chain of its products. "We also check what carbon footprint our products leave behind when they are used by the customer," says Müller. This also includes intelligent fleet management to optimise processes and vehicle deployment, and to keep fleets as small as possible. Frank Müller: "Many customers have to meet their own emissions requirements when planning their fleets. This is where we can make a difference with our broad product portfolio and many years of experience in the refurbishment sector." STILL has also set itself clear goals for the future: compared to the figures from 2017, STILL has so far saved 30 per cent energy in production. The aim is to maintain this figure in the future. And here, too, Müller attaches great importance to transparency: "This is not about headlines, but about concrete activities that lead to tangible and measurable changes." And to a truly circular economy.
Frank Müller talks more about circularity in the BVL podcast. Click here for the full interview: Read more.
Contact request
Subscribe to the Newsletter !
Always up to date with STILL: Subscribe to the STILL newsletter and we will inform you regularly about interesting industry topics.